maxon Inside
陶瓷的最佳状态
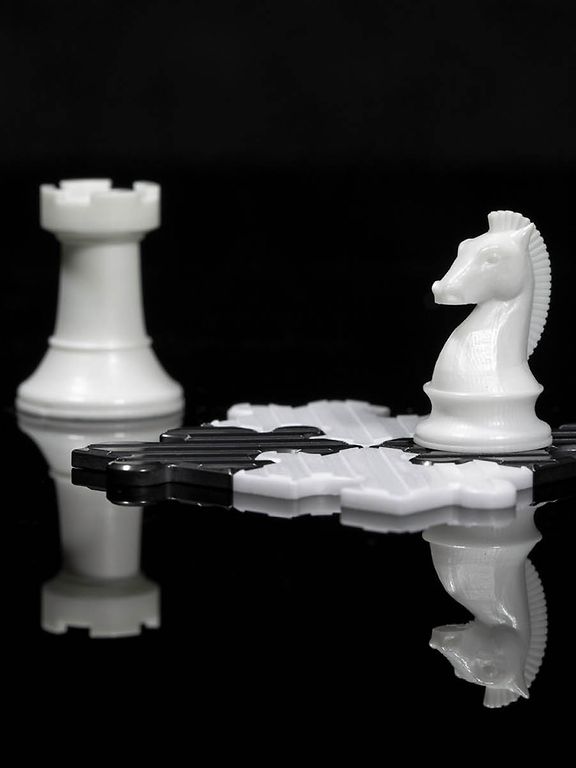
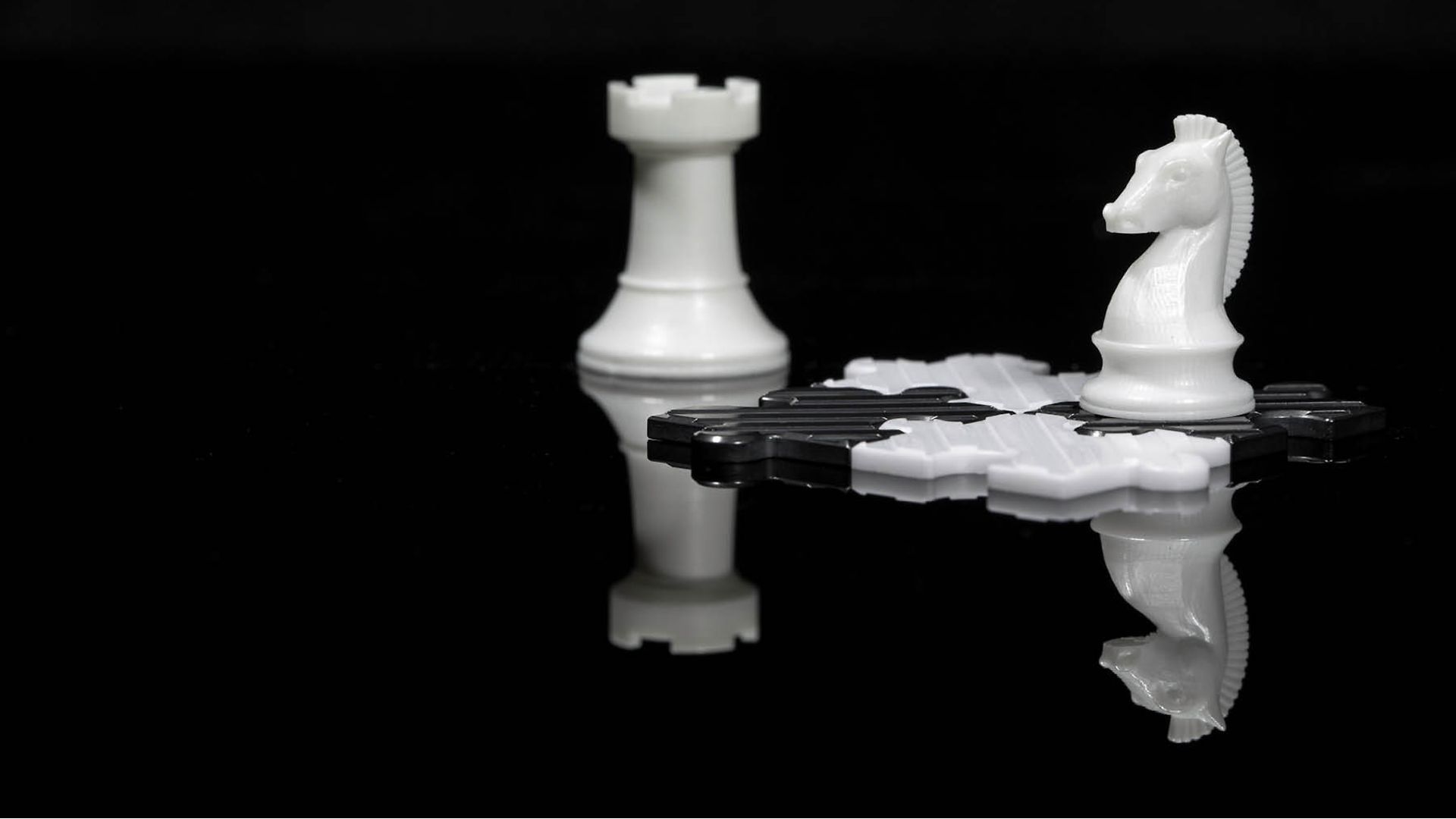
陶瓷部件的增材制造方法可加快原型部件的生产,并开创了全新的可能性。
瑞士maxon公司以其驱动技术而闻名世界,这家公司的技术产品已搭乘美国国家航空航天局 (NASA) 的各种火星探测车一路飞往火星执行任务。然而,公司中位于德国弗莱堡附近塞克绍 (Sexau) 的高科技陶瓷部门却并不广为人知。在这里,现在也可以利用3D打印技术打印陶瓷部件,然后使用激光进行完善。
“有什么材料甚至比钢更耐磨,可制成行星齿轮箱的转轴和轴,从而使行星齿轮箱更精确和可靠?”早在20多年前,驱动装置专业公司Maxon Motor GmbH的专家们就已经探讨过这样的问题。在位于塞克绍的CIM/MIM能力中心,业务发展和质量工程主管Stefan Zilm如今已知道这个问题的答案:采用陶瓷注射成型技术生产的陶瓷部件,这种工艺与金属注射成型技术类似。
如今,这家公司在技术陶瓷产品领域已经拥有非常丰富的专业知识技术。采用CIM技术可以大批量生产数万个部件。然而,尽管拥有丰富的经验,即便采用的是最先进的工程设计方法,比如CAD、有限元计算和仿真等,现实始终是对一种新创意的最终考验,它决定了这个新创意是否合理,或者陶瓷部件是否可按计划生产和运行。
一般来说,从创意到真正成为陶瓷部件的道路不仅漫长,而且成本极高。比如,需要一个造价极高的模具来制造要进行烧结的生坯。接着,还需要借助工作密集型的工艺,对生坯进行车削、切割、烧结和打磨。Zilm承认:“对于第一件样品来说,这个过程真的非常复杂,需要投入大量的时间和金钱。”
使用打印机加工陶瓷部件
但还有另外一种选择:3D打印提供的快捷方式,使得3D打印这种技术已在塑料部件加工领域内得到广泛应用,如今甚至越来越多地被用在金属加工领域中。尽管塑料和金属打印已在工业生产中应用已有好几年的时间,但陶瓷打印还处于从实验室到工厂的冒险阶段。但是,陶瓷打印所带来的优势极具吸引力,因此maxon在五年之前就已开始进行试点测试,旨在以更快的速度将陶瓷部件原型送到客户手中,同时也完成一些真正的开创性工作。Zilm:“有了这样一款打印机,就能更加简单、更加快速地完成初期的两三个开发循环。”
经过深入的市场调研,maxon最终决定选择法国制造商3DCeram提供的打印机,这款定制打印机可以满足公司生产的特殊要求。“对我们来说,最主要的亮点就是精度以及300乘300毫米的超大打印面积”,Zilm解释说。这款打印机基于立体光刻法,这种方法通过激光固化由陶瓷粉末和粘结剂组成的乳液,并从下到上逐层构建部件。每一层的厚度在0.025至0.125毫米之间。打印完一层之后,打印机床便向下移动一步。这样不仅可以确保材料在固化过程中均匀收缩,而且能保证高精度和非常精细的细节渲染。打印时不需要支撑结构。3DCeram系统的特殊优势在于:它可以制造体积仅50立方毫米极小型部件。
根据具体要求,陶瓷部件通常采用锆和氧化铝制成。这些材料在技术陶瓷加工领域中就是像“面包和黄油”一样绝配的材料。两者都可作为3D打印机的乳液使用。脱除粘结剂和烧结技术与CIM工艺兼容,因此在3D打印机中构造的生坯也可以使用大批量部件的生产系统进行加工。根据所需部件的复杂性和要求的公差等级,也能进行小批量生产,因此是陶瓷注射成型 (CIM) 的良好替代品。
按照Zilm的说法,由于紫外线激光束直径的原因,这种工艺确实有其局限性,因此紫外线激光束的直径决定了可以生产的最小壁厚。使用压缩空气和添加剂来清洁部件,可以去除部件上多余的材料。尺寸等于和小于0.5毫米的孔不能像采用注射成型技术时那样完美地形成圆形,但对于原型来说,这通常已经足够了。
从一开始就是研发合作伙伴
如今,客户只需要发送一个在3D打印中常见的标准STEP格式文件(产品模型数据交换标准),很快就能获得报价。在确定订单之后10到14天内,客户就可以拿到第一个原型件。“过去,单这个过程就需要几周甚至几个月的时间,而且模具成本非常高”,Zilm回忆说。
在理想情况下,客户从一开始就与maxon共同进行研发。“从最初创意开始,我们就成为研发合作伙伴,因此可以参与和影响设计,从而尽可能使其适合陶瓷”,Zilm解释说。正因如此,才可以将比如多个部件组合成一个部件,以优化功能性。Zilm表示:考虑到生产陶瓷所需商品的价格约为钢铁的十倍,因此这样的优化非常重要。“我们必须通过提供明显更优异的功能来证明这一点,例如通过增强耐磨性、温度稳定性或不需要润滑剂。”
然而,这还远未达到增材制造的极限。CIM/MIM能力中心负责人Andreas Philipp确信:“我们必须学会以3D方式思考,而不是像以前那样以传统方式思考。”这样,以后一定会出现全新的可能性,因此3D打印极有希望成为目前各种既定工艺的真正替代方案。